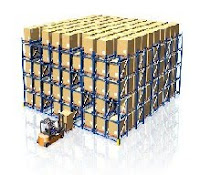
Nel post precedente abbiamo tratteggiato quali risultati si possano ottenere dalla gestione ottimale delle scorte, valutando che esse sono sia un costo che un’opportunità per l’azienda.
In questo post analizziamo più nel dettaglio il metodo da impostare per ottenere proprio questo miglioramento nella loro gestione.
In questo post analizziamo più nel dettaglio il metodo da impostare per ottenere proprio questo miglioramento nella loro gestione.
Come è noto, le principali finalità di un buon sistema di gestione delle scorte sono due:
- assicurare all’utilizzatore l’esistenza a magazzino (disponibilità) dei materiali necessari all’attività industriale nel momento in cui essi necessitano;
- contenere al minimo i volumi di merce giacente (immobilizzi), gli oneri di gestione (costi di magazzino) e quelli di conferimento degli ordinativi ai fornitori (costi di approvvigionamento).
Tali contemporanee finalità, di per sé contrastanti, possono essere conciliate mediante l’uso combinato di metodologie specifiche e di strumenti opportuni, che permettono a loro volta di agire su due fronti:
- pianificare gli approvvigionamenti dimensionando i fabbisogni di materiale sulla base di analisi statistiche, storiche e previsionali, ed effettuare i riordini a cadenza programmata;
- gestire il magazzino in logica di flusso tenendo sotto controllo continuo gli specifici indici gestionali (indici di rotazione, livelli di scorta minima, lead time dei fornitori, eccetera).
La scelta della logica di pianificazione dei fabbisogni dipende da fattori locali, differenti per tipo di azienda e di processo di trasformazione, migrando dal classico modello MRP (Material Requirement Planning, che mette in fila gli «appuntamenti» a ritroso partendo dalla data prevista di disponibilità finale e arrivando a definire le singole date iniziali di emissione degli ordini di approvvigionamento) al più evoluto concetto di «transito a flusso», derivante dall’applicazione della metodologia JIT.
Il buon senso comunque insegna che la prima cosa da farsi è la suddivisione dei materiali per fase a ciclo (materie prime, semilavorati, componenti finiti) e per categoria di utilizzo (consumo corrente, per commessa, ricambistica, articoli declassati e scarti, ausiliari, ecc.).
Bisogna quindi definire e dimensionare correttamente per singolo codice i valori dei parametri caratteristici (consumo annuo, giacenza media, classificazione ABC, Lead Time di approvvigionamento, unità di imballaggio, lotto di approvvigionamento o di produzione, livello di scorta di sicurezza, punto di riordino, eccetera), secondo gli algoritmi di calcolo e di contabilizzazione standard proposti da qualsiasi procedura informatica dedicata.
Occorre poi fare il bilancio di convenienza costi / opportunità.
Si sa che il rischio è insito in ogni scelta, compresa quella di mantenere o meno livelli cautelativi di scorta. È importante quindi valutare i pro e i contro di una possibile decisione a riguardo, anche attraverso una semplice stima delle implicazioni economiche a fronte di azioni tecniche. Occorre individuare un punto di equilibrio, che si trova in corrispondenza al valore minimo della somma dei costi da sopportare in funzione del livello di garanzia del servizio che si richiede alla presenza di scorte.
Un chiaro esempio su quanto esposto può essere costituito dal metodo conosciuto come matrice incrociata ABC scorte-fatturato, applicabile a qualsiasi tipologia di scorta e finalizzato a ricavare una serie di indicazioni utili sia per ritarare le politiche di gestione delle scorte che per ridurre il valore del montescorte.
Un chiaro esempio su quanto esposto può essere costituito dal metodo conosciuto come matrice incrociata ABC scorte-fatturato, applicabile a qualsiasi tipologia di scorta e finalizzato a ricavare una serie di indicazioni utili sia per ritarare le politiche di gestione delle scorte che per ridurre il valore del montescorte.
In pratica, classificando il fatturato secondo il criterio ABC della nota legge di Pareto, si ottengono tre categorie di prodotti approssimativamente così suddivisi:
- classe A: il 20% del numero di codici costituisce l’80% del valore di fatturato;
- classe B: il 30% del numero costituisce il 15% del valore;
- classe C: il restante 50% del numero costituisce il residuo 5% del valore.
Applicando lo stesso processo di calcolo al montescorte (valore di giacenza media dell’anno per codice) si ottengono tre categorie analoghe alle precedenti (A = 20% del numero di codici pari all’80% del valore di montescorte). A questo punto «incrociando» le due classificazioni si ottiene l’appartenenza di ogni singolo codice ad una delle nove possibili combinazioni di classe scorte-fatturato, da AA (classe A di fatturato, classe A di scorte) ad AB, AC, BA, ecc. fino a CC.
Si può dimostrare che ognuna delle appartenenze risultanti evidenzia situazioni ben precise e propone soluzioni quali ad esempio:
- classi AA e BA: gestione ottimale prossima a metodologia Just in Time;
- classi AB, BB, BC: consigliata la gestione a punto di riordino;
- classe AC: consigliata l’eliminazione del prodotto (in alternativa gestione per commessa);
- classi CA e CB: necessita il controllo continuo e sistematico dei parametri caratteristici;
- classe CC: nessun problema di gestione.
Non va dimenticato che la matrice è dinamica, cioè variabile nel tempo. È quindi consigliabile utilizzarla periodicamente, per verificarne le modifiche di contenuti per classe. Ed è proprio dallo studio di queste migrazioni interne che si sviluppano le azioni più efficaci di miglioramento della gestione e di riduzione delle scorte.
Queste considerazioni, sempre opportunamente interpretate, forniscono sempre una traccia di come impostare la gestione scorte nei casi reali.
Buona logistica!
il primo a classi dovrebbero essere uniti in una sola classe
RispondiElimina